Energética Magazine: Artificial Intelligence (AI) and Deep Learning as the future for O&M focused on improvement for operators, reduction of labor risks, and sustainability.
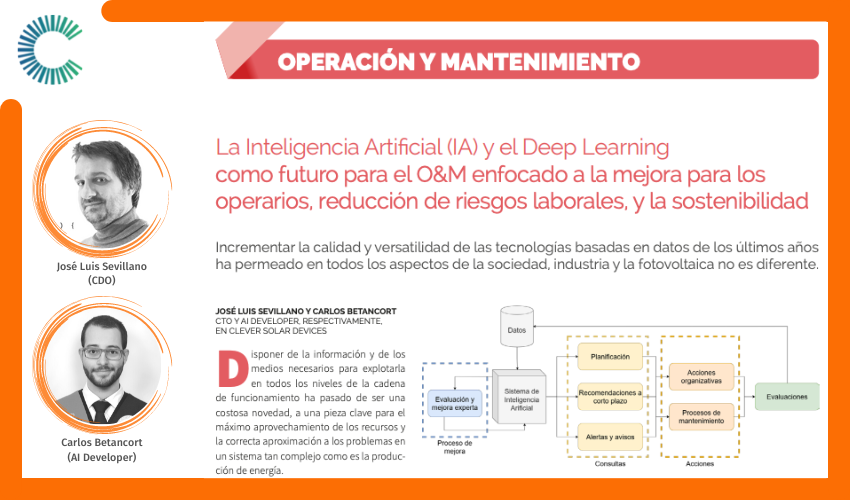
25.11.2022
(José Luis Sevillano - CDO & Carlos Betancort - AI Developer)
The increase in the quality and versatility of data-driven technologies in recent years has permeated all aspects of society and industry, and photovoltaics is no different.
The availability of information and the means to exploit it at all levels of the operating chain has gone from being a costly novelty to a key element in maximizing the use of resources and the correct approach to problems in a system as complex as energy production.
However, due to their technical nature and specificity, added to the fact that every good new technological concept attracts attention, especially if it promises to "reduce costs" or "minimize losses" as if by magic, it is very easy to lose sight of what effect they can have on a real installation.
AI and machine learning systems make it possible to extract knowledge from the data we collect from the real world, crystallize it inside as measurable parameters, and build tools capable of leveraging this knowledge through automated decision making and data interpretation. The quality of the data used to feed the algorithms will be a key factor to obtain accurate and realistic conclusions.
In conventional maintenance, data is collected to perform a diagnosis or review of the system every time we want to obtain a result. These data are analyzed by experts, and the conclusions are translated into practical decisions that can be implemented in the plants by the operators. The chain is set in motion under the demand for results, and each link depends on the result of the previous one. AI can streamline and optimize the process, through the availability of knowledge.
This system will use all available information from our facility to generate results allowing experts to spend their time not analyzing a subset of this data and making a point decision, but to iteratively improve as the system learns allowing conclusions to be generated on demand, making it possible to have the necessary information available, with the assurance that it is based on all available data, remotely and in real time without the need to physically travel to the plant and/or make decisions based on indirect measurements (e.g., drone thermography or production-based estimates).
The closer the measurement data is to what is to be identified, the more accurate the results will be. In the case of PV module diagnostics, IV curves lose quality the further away from that value the information collected is, or the more indirect the measurements are.
What are the benefits of having this kind of information? Its main manifestation is at the most physical and tangible level, the manipulation of the hardware by the operators. For example, in the diagnosis and repair of a plant with suboptimal production, operators can approach the problem by handling all the information in advance and being able to design better intervention strategies, knowing not only which modules are specifically failing but also what type of failure they are reporting, diagnosing remotely, and reducing the risks linked to manual maintenance. When performing repairs, this system (the one used by Clever Solar Devices) alerts operators to prioritize modules with dangerous characteristics (unusual electrical or thermal measurements), and run a complete and accurate pre-diagnosis of these, to speed up the work and efficiency of maintenance.
Knowing the status of our plant with this level of detail allows us to organize and plan the initial action protocol of the equipment, as well as make decisions such as the feasibility and efficiency of executing a repair versus its cost in resources, predictions of degradation in the future and even retroactive studies to locate and document problems occurred, to improve. This detailed information enables better decisions to be made, and resources to be used efficiently, reducing occupational hazards such as electrical and thermal shock or falls from heights.
Having this data in real time, allows to raise maintenance operations to another level, improving efficiency and generating more clean energy and reducing CO2 levels.
At Clever Solar Devices we consider all these principles in the design of our algorithms, as part of our commitment to the overall improvement of the quality of the installations.