Energética - PHOTOVOLTAICS 4.0
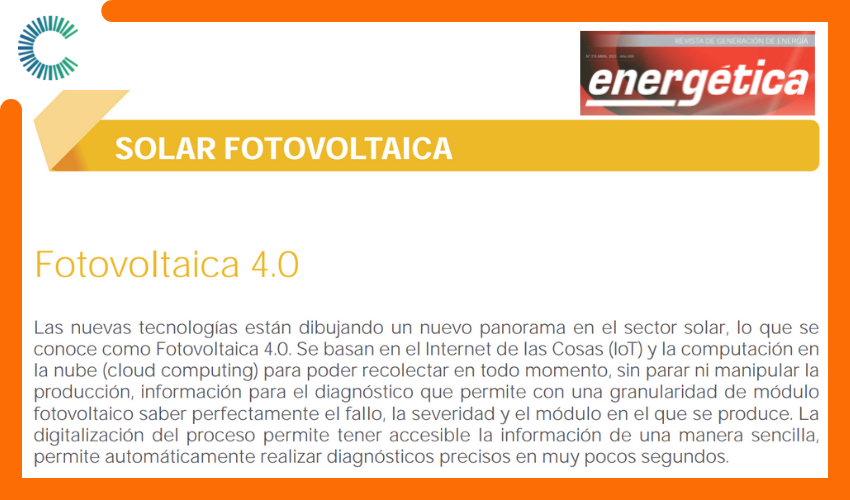
27.04.2022
Solar photovoltaic (PV) energy is one of the key resources to evolve into an energy. Thanks to technological developments, it has been possible to improve processes, reduce costs and significantly improve efficiency. Solar modules with efficiencies of over 20% can be found commercially and already exceed 46% in the case of laboratory experiments. Efficiency is closely related to generation power. The better maintained a panel is, the more efficient it is. Therefore, knowing in real time the status of a photovoltaic module is key to generating maximum power. To illustrate the example, let's do a simple math: Solar power = 1000W/m2, reference module efficiency 20.7%. If we take a panel size of 2.094m x 1.038m = 2.1735 m2 the solar module will have an area of 2.1735 m2. Applying simple mathematics, we will have that the solar panel has a power of 1000 x 2.173 x 0.207 = 450W.
As technology evolves, the price of solar panels decreases, but the opportunity cost increases drastically if the panel stops working. The opportunity cost is the losses that occur due to all the energy that we will not be able to generate and therefore use if the panel is in poor condition.
In 2020 there was a total installed power of 773GW. Continuing with the example of the module that we have taken as a reference and imagining that all the power worldwide is produced with the latest technology panels, we have that there are 773,000,000,000,000W / 450W = 1,717 million panels in the world, corresponding to an area of 1,171 x 2.17 = 3,733 million square meters. If the modules were in vertical position forming a line, we would have a distance of almost 18,000km. Spending only one minute on each of the modules and only once, a total of 3805 years would have to be spent to check each of them.
To reduce the opportunity cost it will be of great importance to use strategies to detect failing modules at an affordable cost, and the magnitude of the problem is large, and getting larger all the time.
There are a large number of indirect methods that aim to partially speed up the detection of such failures. We call indirect methods all those that use one quantity to determine another.
- Manual processes with drone thermography: Drone thermography is inaccurate and indicates only "hot spots" that subsequently require manual inspection involving stopping production and manipulating the PV module cables to connect them to the measurement device and extract the IV curve of the modules (the most accurate information for diagnosis). The measurements must be stored manually in the SD memory for later downloading and analysis. Any possible human failure could involve critical occupational hazards and affect the reliability of the data.
- Dataloggers: These are generic instruments whose measurements are based on production. Normally, these measurements are complementary to the main function such as inverters (transform DC to AC) or MPPT (find the point of maximum working output). The instrumentation automatically measures physical values.
- Monitoring Platforms: These are based on third party output measurements from the datalogger. There is no measurement control or data accuracy for diagnostics. Diagnostics are based on output (single value voltage and current) requiring AI algorithms and historical information to approximate possible faults present. platforms are remotely accessible and flexible. Diagnostics are based on estimates, not on actual measurements of each module.
Photovoltaic 4.0: The IV curve at panel level is the only method that allows to diagnose in a univocal way a problem in the solar modules. Therefore, thermography that measures temperature to see electrical problems, electroluminescence using the emission of light radiation, reduction or deviations in production to highlight possible faults are considered indirect. All indirect methods have in common that they must be complemented with manual measurements, sampling part of the installations and that due to the time they take, it is done once or twice a year.
In this sense, new technologies draw a new panorama in the sector, what is known as Photovoltaic 4.0. They are based on the Internet of Things (IoT) and Cloud Computing to be able to collect at all times, without stopping or manipulating the production, diagnostic information that allows with a granularity of photovoltaic module to know perfectly the failure, the severity and the module in which it occurs. The digitization of the process allows to have the information accessible in a simple way, allowing automatically to perform accurate diagnostics in a few seconds. Digitization at the PV panel level makes it possible to automate the tracing of IV curves, which would mean moving from a scenario in which the diagnosis could cost 3805 years, to one in which all the detailed information would be available in a few seconds.
Photovoltaic 4.0 is already being tested by large companies in the sector and is the proposal of companies such as Clever Solar Devices that offer a technological leap to minimize the complexity of maintenance tasks in installations.